|
|
Javascript DHTML Drop Down Menu Powered by dhtml-menu-builder.com
History
MetaLL ife was developed 1983 to extend the life of cutting tools, particularly taps
and drills. When the benefits of doing
MetaLL ife to taps was confirmed
thousands of times in the field, the process was tried successfully on other types of cutting tools, including drills, endmills, milling
cutters, geometric chasers, etc.
One of our cutting tool customers was also a tool shop for
building die cast tooling. The tool shop had a customer that was having premature
die fatigue cracking.
MetaLL ife
was applied successfully on a tool. The rest is history.
The technology has been improved and modified
over the years. In the case of plastic molds (H-13 or hot work
steels),
MetaLL ife
can be polished to the required mirror finish without losing the compressive
stress benefit. Today the process is being applied with equal success in the Drawing/Forming/Blanking
markets.
MetaLLife
was introduced in June 2001 to address die casting inter-metallic soldering
issues.
ThermaLLife
has shown die casters that there is an effective way to stop the adhesion of aluminum to die steel). Dies for plastic that mold
abrasive glass and fiber additives or chlorinate based PVC materials
will no longer be attacked by corrosion and heat checking that shortens the
life of all H-13 plastic molds. Thermoset plastic molders have a lower cost and viable
alternative to the expense of repeatedly polishing, coating, stripping,
polishing, coating, stripping, etc...
ThermaLLife
will not affect the smooth finish required in most plastic tools. Testing
is underway in 2010 to confirm these facts both in the lab and field trials.
Another market that is being explored,
starting in 2010, is hot forging.
By utilizing and combining
MetaLL ife,
ThermaLLife,
and Tungsten Carbide deposition to the surface of hot forging tool (also made
from H-13), the porosity that is usually present with this deposition is
reduced. By this Badger may be able to significantly extend this industries tool life
as well.
"Prior to
MetaLL ife,
a die caster's only alternative to repairing was to weld the tool, resink the tool, or build a new die...all of which are costly and
progressively more extreme procedures.
For over a quarter of a century, Badger
Metal's technology and its
dynamic team of knowledgable employees has educated die casters by showing them a less costly and more
effective alternative to be both proactive and reactive with their
maintenance programs. Our roots are planted in the die casting
industry with new growth that includes customers in the plastic and the
drawing/forming/blanking industry. We continue to mature by close
association with NADCA, (North
American Die Casting Association), the SPE (Society of Plastic Engineers) and
the PMA
(Precision Metal Forming) trade organizations. |
|
|
|
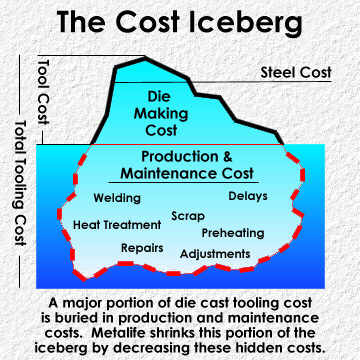
A major portion of tooling cost is hidden in
production and maintenance costs.
We can shrink the bottom
portion of this iceberg by decreasing these hidden costs.
|
|
|