|
|
Javascript DHTML Drop Down Menu Powered by dhtml-menu-builder.com
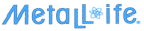
Applications
Javascript DHTML Drop Down Menu Powered by dhtml-menu-builder.com
Die
Casting Dies - NEW, USED, WELDED, POLISHED
Die casting dies
because of temperature gradient thermal shock, develop high levels of
tensile stresses in a short amount of use time. Sometimes micro
cracking can develop in as little as 10-100 shots. By applying
MetaLLife
when the tool is NEW,
and once again at the existing historical HALF life, a minimum increase
of 25% can be observed. It is recommended that, if possible, the
tool should be processed before any molten metal has contacted the
surface of the die.
Die casting dies that are
USED
and have developed some thermal heat
check cracks may be candidates for
MetaLLife
depending on the size and depth of the cracks. In these instances
it is best to send a recent casting that will provide a fingerprint of
the operating condition of the die including any cracks that have
developed. Even if the cracks are too large to close, the
compression benefit at each end of the crack will slow further
propagation. Gross cracking and cavitation breakout cannot be
repaired using
MetaLLife.
Die casting dies that are
welded have an inherent high level of
tensile stress. Residual tensile stress from welding is
created because the weld consumable is applied in its molten state. This
is its hottest, most expanded state. It then bonds to the base material,
which is much cooler. The weld cools rapidly and attempts to shrink
during the cooling. Because it has already bonded to
the cooler and stronger base material, the weld is unable to shrink.
The net result is a weld that is, essentially, "stretched" by the
base material. Inconsistencies in the weld filler material, metal
chemistry, weld geometry, porosity, etc..., act as stress risers. These
residual tensile stress conditions start further initiation of premature die
fatigue failure. The weld negatively affects the integrity of tooling.
Common practice is to perform a subsequent stress temper to remove these
stresses.
MetaLLife
is beneficial in reversing the residual stress from welding that tends to
cause failure. These stresses in the die cast tool's heat affected
zone are converted to a beneficial compressive state. The above
graph shows the "as welded" condition and then the reduction in tensile
stress when only a stress temper is performed and finally the
compressive benefits induced after
MetaLLife,
and a prior stress temper. Tensile stresses generated from welding
are additive with applied load stresses. This is why these "as
welded" combined stresses accelerate failure at welded locations.
Heat stress tempering to reduce the tensile to zero (approximate) then
following with
MetaLLife,
restores the integrity of the weld and its relationship with the base
material.
A relatively new
procedure to reduce fillet and radii cracking of die casting dies is now
known and practiced by a limited number of informed die casters (introduced in
2008). The procedure involves a
diamond polish to these specific areas as opposed to finishing them with a
300-400
stone. When
MetaLLife
is applied before the diamond polishing, the effective fatigue resistance
in these areas can be increased 30-40%. Field trials and
production usage have shown increases in tool life from 38% to over 100%.
There is no concern about reducing the compressive stress benefit since
a higher resulting fatigue protection is revealed after polishing due to
the knee shape of the compression curve.
See resource section of our site for more information.
Drawing,
Forming, Blanking Dies
Blanking
and piercing dies fatigue
at sharp corners. This requires them to be frequently reground to
restore the sharpness. By applying
MetaLLife,
the frequency or need to do this is reduced or eliminated. The
process is applied without damaging existing sharpness of the tooling.
Drawing and Forming
dies have a tendency to gall
and pick up material during use. Coatings and plating make the
surface slicker, however, applied lubricants do not adhere very well.
With use, the coating can wear and must be reapplied.
MetaLLife,
before coating, will provide a topography to the surface on a micro level
that retains lubricant. When this is combined with the coating or other surface
treatments, it enables these dies to perform at maximum efficiency.
Related Topics
> - Benefits |
|
|
|
USED
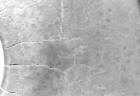
Before
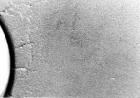
After
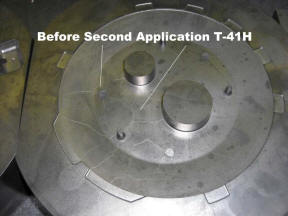
Click for larger views
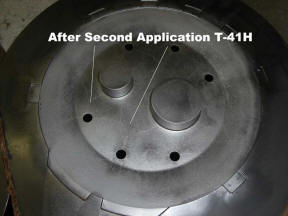
USED - Second Application |
|
|