Automated Measurement System for Gas
Nitriding and Nitrocarburizing
Vytas
Braziunas, Automation Intelligence LLC, Milwaukee, Wis., Leo Porkka,
Metallurgist, Milwaukee, Wis., and Daniel H. Herring, The HERRING GROUP,
Inc., Elmhurst, Ill.
Measurement of the ammonia dissociation allows for
an improved understanding of nitriding and nitrocarburizing processes,
as well as process repeatability and precise parameter adjustment. A new
advanced control system allows optimization of gas use and case
microstructure.
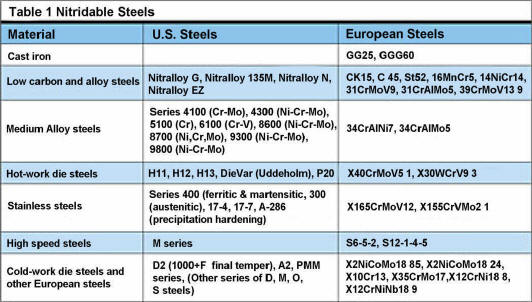 |
click on above
table for printable view |
Nitriding and nitrocarburizing are surface
treatements intended to
increase surface hardness and to improve other properties of tool steels such
as those listed in Table 1. One of the appealing attributes of this
thermo chemical ferritic nitrocarburizing (FNC)
process is that rapid quenching is not required; hence, dimensional
changes are kept to a minimum. Nitriding and nitrocarburizing benefits
include:
- Ability to streamline the manufacturing cycle by eliminating
processing steps.
- Exceptionally high surface hardness
- Resistance to wear, anti-galling properties (good in poor
lubricating conditions), and the reduction of soldering tendencies in
die cast and aluminum extruding operations.
- Minimal distortion and deformation compared with
carburizing/hardening
- Resistance to tempering; resistant to softening up to nitriding
temperature at which conventional steels soften
- Stable nitrided case
- Improved fatigue life and other fatigue-related properties such as
fatigue strength (resistance to dynamic loading)
- Reduction in notch sensitivity
- Marked resistance to corrosion in several common media (except for
nitrided stainless steels)
- Small volumetric changes (some growth does occur)
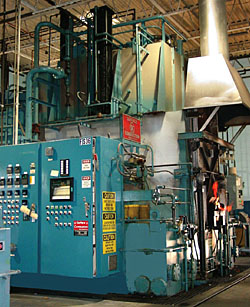 |
Fig 1. Modern gas nitrocarburizing furnace |
Nitriding and nitrocarburizing surface treatments have been used
increasingly over the past decade. Non-gaseous processing methods, such
as salt and plasma nitriding, have not reduced the interest in gaseous
nitriding/nitrocarburizing, primarily due to the flexibility in
processing parameters, which allows achieving an optimized
microstructure to meet treated component application requirements. These
one-step processes are replacing two- or three-step conventional
processes, such as carburizing or carbonitriding followed by grinding
and/or plating, due to benefits such as minimal dimensional change and
high surface hardness. However, there are currently a substantial number
of furnaces in use that do not have adequate process measurement and
control systems, which are required to meet the demands of today's
customers.
Innovative commercial heat treat companies are
improving furnace atmosphere control by adapting state-of-the-art
temperature and atmosphere controls, which provide continuous, precise
regulation of the process in progress (Fig.1).
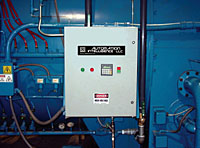 |
Fig 2. Automatic nitriding potential
measurement system |
Three major benefits of control systems based on automatic nitriding
potential measurement compared with traditional open-loop furnace
control, where predetermined amount of gas is pumped into the furnace
over certain amount of time are:
-
Reliable measurement of nitriding potential, which enables a
repeatable process and prevents the degradation of processed part
quality caused by hard to control circumstances, such as failing
seals
-
Automatic control, which offers the ability to use just the right
amount of gasses, lowers the processing cost and minimizes
emissions
-
Optimal nitriding potential level, which allows processed parts to
meet case specifications and controls the growth of the white
layer
Limitations of existing control
methods
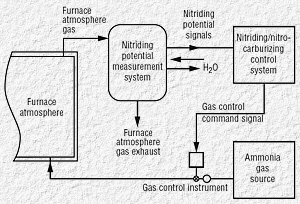 |
Fig 3. Nitriding potential measurement system
block diagram |
Several methods of automated measurement of nitriding potential or
ammonia (NH3) dissociation percentage in a heat-treat atmosphere are
being used, usually consisting of photometry of ammonia in the infrared
range while ammonia is still in gaseous form. The principal of infrared
photometry is based on measuring the intensity of infrared light
transmitted, absorbed or reflected from a gas sample and comparing the
results with a reference light intensity. Disadvantages of this type of
process include interference of other gases in the mixture, drift of the
instrument, the need for frequent calibration and expensive span gas.
One of the biggest obstacles of using infrared nitriding potential
measurement in the heat-treat production environment is the necessity to
have extremely rigorous maintenance procedures in place to keep the
optics and sensors clean.
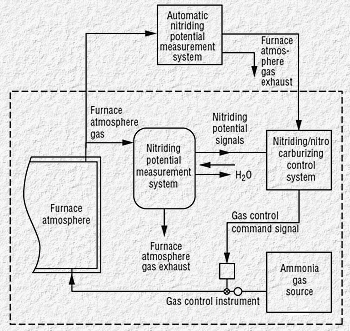 |
Fig 4. Nitriding control system with multiple
sensors diagram |
Another automatic nitriding-potential measurement method involves
determining the individual gas concentration in a mixture of gases by a
thermal reaction heat measurement, where the heat is generated by
ammonia being burned on a catalyst. This approach is also difficult to
perform reliably in an industrial setting.
Another method involves determining the concentration of gases that
are a product of dissociated ammonia (such as hydrogen) and calculating
actual dissociation. This approach also uses sensors that can drift,
which gives false readings, and that are not always able to endure the
harsh furnace environment.
One of the most widely used nitriding potential measurement of the
gas mixture is a manual sampling method. This is performed by capturing
a predetermined amount of gas in a special ammonia dissociation
measurement burette, then dissolving ammonia in the gas form into a
liquid form, and determining the concentration of ammonia in solution by
visually measuring the level of water. Problems with this measurement
method are fragile equipment, difficult visual extrapolation and
interpretation of the water level measurement, which make manual burette
measurements challenging to use in an industrial setting, but it remains
a measurement of choice for a wide variety of furnace operators.
New automatic measurement
system
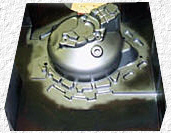 |
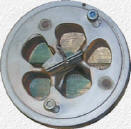 |
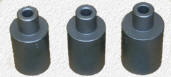 |
Tool Steel Examples
Fig 5. Left - Hot-worked
H-13 die casting die
Middle - Hot worked H-13
aluminum extruding die
Right - M2
punches |
A new automatic nitriding-potential measurement system (Fig. 2) based
on dissolving ammonia in water has been designed to improve existing
furnace controls. The system is installed and operating at a commercial
heat treating company in Milwaukee, Wisconsin. In
addition to sensing nitriding potential, the system also generates
process alarms and provides closed-loop ammonia control within the
heat-treating furnace.
System description and operation
Increasing process-quality challenges require operator-friendly
measurement devices, which removes operator-induced variability, while
requiring minimal maintenance. The automatic system (Fig. 3) performs
the measurement and allows the operator to adjust process variables
manually or automatically according to a pre-set program.
The system-engineering goal was to design a robust,
stable system that could survive harsh plant environments, while
providing continuous, accurate and easy-to-define process measurement.
The high accuracy and repeatability requirements of processes
presented even greater challenges.
The nitriding potential-measurement system is set-up to automatically
sample the furnace atmosphere. The main measurement chamber is equipped
to receive the true processing atmosphere that exists in the
nitriding/nitrocarburizing furnace. The measurement chamber is also
equipped with water inlet and outlet lines and atmosphere exhaust line.
Water for precision measurement is supplied from a specially designed
constant low-pressure water vessel. The water is used to process furnace
atmosphere gas samples and to calculate the nitriding potential. During
the measurement cycle, the water flow and volume required for full
ammonia dissolution is measured using electronic sensors, which generate
signals that are converted by a digital controller into process
information. The measurement result is automatically logged and
instantaneously reported to a furnace operator. The information can be
presented in multiple formats, such as nitriding potential, percent
residual and percent dissociated ammonia.
Nitriding-potential information is sent to the
nitriding/nitrocarburizing control system, which allows adjustment of
gases flowing in the furnace based on the input. An automatic
self-calibration procedure is a unique characteristic of the system,
which is especially critical when processing expensive workloads.
Automatic self-calibration can be performed according to a pre-set
schedule, or initiated by the operator as needed, does not require
certified gases and is based on a precise measurement of the known
vessel volume.
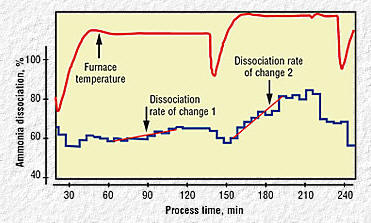
Fig 6
|
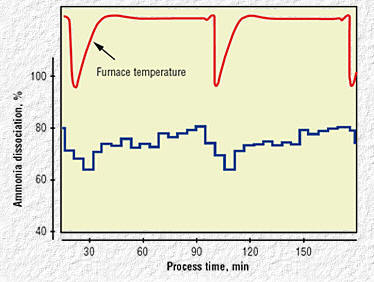
Fig 7
|
Fig 6. Process temperature and ammonia
dissociation measurement example
Fig 7. Excess ammonia
supply |
Multiple sensors increase reliability
Automatic nitriding-potential measurement offers the use of multiple
sensors to augment existing sampling or in-situ systems for increased
accuracy and control reliability. This aspect of the nitriding-potential
measurement determined using the new automatic gas dissolution in water
method is comparable to ammonia measurement results achieved using other
measurement methods.
This combination system with redundant capability (Fig. 4) offers
high reliability and continuous availability compared with a single
sensor control system. Sensing deviation from other sampling or in situ
automatic systems can be also minimized by using the multisensor
system's self-calibration feature.
The new measurement system is suitable for use with integral quench
furnaces, fluidized bed furnaces, pit furnaces and retort furnaces, and
can be used to monitor and control ammonia dissociator performance.
Process gas-sampling frequency is adjustable and can be set up by the
operator to achieve optimal control over the full processing cycle.
Process measurement and control
examples
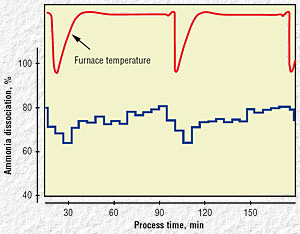 |
Fig 8. Controlled ammonia dissociation
process chart |
Commonly nitrided and nitrocarburized part include
components made of plain or medium carbon, low -alloy steels used in
automotive, agricultural, hand tool, lawn and garden and medical
applications. Other uses in the tooling area include hot work and cold work tool steels for applications in die
casting, drawing/forming/blanking, and aluminum extruding dies. Fig. 5
shows applications for die casting, aluminum extrusion, and heading
punches.
To establish a baseline of the processes being measured and
controlled, a number of tests were performed in a batch furnace using
the new ammonia measurement and control system. Furnace temperature and
ammonia dissociation information (Fig. 6) were recorded for two process
cycles. The ammonia flow in the furnace was kept constant, while the
temperature was set at two different and subsequent higher temperatures
during the first and second cycle times.
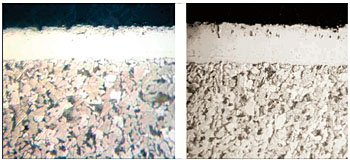 |
Fig 9 -
Microstructure of part processed using constant ammonia flow method,
left, and microstructure of part processed using reduced ammonia
flow, right. |
Tests were performed (Fig. 8) to determine the optimal amount of
ammonia to produce the desired processed part characteristics. When the
dissociation of ammonia is decreasing, the possibility exists that
excess ammonia gas is being supplied to the furnace. Control of gas flow
in this case will allow realizing a substantial gas savings.
Flow control can be implemented after understanding the process
dynamics. Part configuration and surface area must be taken into
consideration when selecting the control algorithms. For the two loads
made of the same material and processed at the same temperature, the
load with the larger surface area will tend to reduce nitrogen activity
more rapidly, as more ammonia molecules dissociate at the larger steel
surface area per unit of time. Figure 8 shows a chart of the controlled
ammonia dissociation during two consecutive batch processing cycles. The
microstructure of the part processed using the common industry method of constant ammonia
gas flow method
is shown on the left side of Fig.9 and that of the part processed using
reduced ammonia flow by the control method is shown on the right side of Fig.
9.
References
1 Principles of
Nitriding and Nitrocarburizing, Atmosphere Heat Treating, Basic Seminar,
Ipsen International, 1998
2 T.G. Diggs, S.J.
Rosenberg and G.W. Geil, Heat Treatment and Properties of Iron and
Steel, NBS, Monograph 88, 1966
3 E.Z. Lehrer,
Elektrochem, V61.36, No.6, p 383-392, 1930
4 K.H. Jack,
Nitriding, Heat Treatment '73, The Metals Society, Book 163, p 39-50,
1975
5 T. Bell, et.al., Controlled Nitriding in
Ammonia-Hydrogen Mixtures. Heat Treatment '73, The Metals Society, Book
163, p 51-58, 1975
6 B.J. Lightfoot and
D.H. Jack, Kinetics of Nitriding with and without White Layer Formation,
Heat Treatment '73, The Metals Society, Book 163, p 59-65, 1975
7 S. Mirdha, Ph.D. Thesis, Univ. of Leeds, 1980
8 T. Bell, Ferritic Nitrocarburizing, Met. Eng. Q., May
1976