|
|
.Javascript DHTML Drop Down Menu Powered by dhtml-menu-builder.com
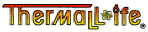
Customer Testimonials
Javascript DHTML Drop Down Menu Powered by dhtml-menu-builder.com
Test Result Comments
(Our
customer comments are numerically coded to protect our clients security and
wishes)
Reduced Soldering
-
#790 - IA - Pleased with
ThermaLLife
performance to date on all tooling processed. Said it's "working good." Also
advised business is good.
-
#955 - AR - In 2007 January, we lost our source for
SolveniteÒ.
ThermaLLife has proved to be an ideal alternative solution which is also less
expensive than our previous lost source.
-
#955 - CO - Core pins would solder after only 500 shots.
Production costs were sky-rocketing due to downtime. After
ThermaLLife
was able to run 5000 parts and finish the run without a single downtime for the
previous problem.
-
#007 - WI - Once used a process similar to this until the local plant
closed. Am glad to see that the technology has improved so that can provide the consistent results that we could not obtain from other
processes. Use it on cores and slides that have a tendency to solder
and/or gall. May try on some problem die casting inserts in the near
future.
-
#054 - IL - Have been using
ThermaLLife
since its introduction in July 2001. Applications to
cores have reduced or eliminated previous soldering problems. Works
equally well on problem molds that have a tendency to solder. Have tried
all the "so called" miracle coatings, platings, and long time chemical
processes but nothing supplies the consistent results of this process.
-
#178 - MI - Spline cores - exceeded what ion-nitriding did previously for
us. Have been able to get over 300,000 shots on the
ThermaLLife
processed cores.
-
#644 - WI - Long time user of
MetaLLife.
Use
ThermaLLife
to reduce soldering. Quite effective at also reducing washout and erosion.
Like the fact that both processes can be re-applied when/if necessary without
any special preparation. Found to be effective and beneficial on dies as
well as cores and slides.
-
#872 - IL - Was one of the first to use the combination process by
applying first
MetaLLife
then
ThermaLLife
on transmission dies. Significant reduction in soldering (which was a
severe problem) and heat checking. Have since applied to an additional set
of new cavities with the same results.
Return to top
Improved Fatigue Resistance
-
#872 - IL - This customer has been able to increase their
tool life for a sensitive automotive part ten (10x) fold by applying
MetaLLife
followed by
ThermaLLife
after final sampling on NEW tooling.
-
#607 - MI - Extremely pleased with the extended life increase of 75% over
the normal 50,000 shots (now 125,000 shots) he was getting. They polish
them almost daily w/ an MX wheel + stone. Continuing to use
ThermaLLife
for the fatigue benefits.
#050 - IN - Usually gets 40,000 out of die cast valve cores. The main
reason for failure is bending and loss of dimensional tolerances, not erosion.
ThermaLLife
cores still running with now over 60,000 shots on them.. Usually get 20-30k out of the piston cores.
8 out of the twelve processed are still running far past this count.
When you don't hear any complaints from the floor, this is usually a very good
sign that what you are doing is working.
-
#266 - MN - A large die casting tool with and established history of heat
checking, washout, and soldering, was processed with
MetaLLife
after it had unknowingly been processed with the Ferritic Nitro Carburizing treatment. After performing better than any
similar tool in our history, it was determined that this tool had, indeed,
received the combination process. We are now believers and planning on
treating all of our tooling this way.
-
#834 - WI - Performed the combination process of:
MetaLLife
+
ThermaLLife
to two different die cast tools with a history of heat checking and fatigue
failure. Both tools went far over their normal life expectancy showing
increases in the range of 50-85%. One tool is still functioning while
running a back to back comparison against an untreated tool. The untreated
tool has 1/2 as many shots as the treated and is being pulled from
production. The treated tool is continuing to produce parts with over
180,000 shots on this die set. Plan on incorporating on more tooling.
Return to top
Less Erosion and Washout
Field test data being reviewed
Return to top
Anti-Galling of Draw Dies
-
#286 - WI - Customer was experiencing a rapid galling problem on some
older tooling used to make medium size drawn part. After
ThermaLLife
customer was able to run a complete run of 500 parts without any problems.
Prior to this die would gall immediately on the first couple of parts and have
to be re-polished many times just to get 500 pieces. Die material is D2.
Due to the known age of this tooling, final temper was performed at the lower
knee point. Most new D2 is being final tempered at 1100 degrees F.
This die was probably final tempered at 500 degrees F.
-
#891 - MO - Performed the process on a used tool that had been welded many
times.
ThermaLLife
performed so well that we did not have to build a new tool as originally
anticipated from all the galling problems we were having prior to
processing.. Continuing to run the tool as is and use the process.
Return to top

Increased Wear Resistance and
Fatigue Strength
Return to top
Related Topics
> - Frequently Asked
Questions |
|
|
|
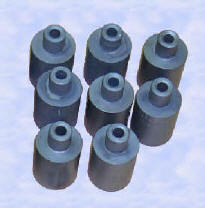
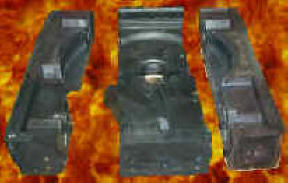
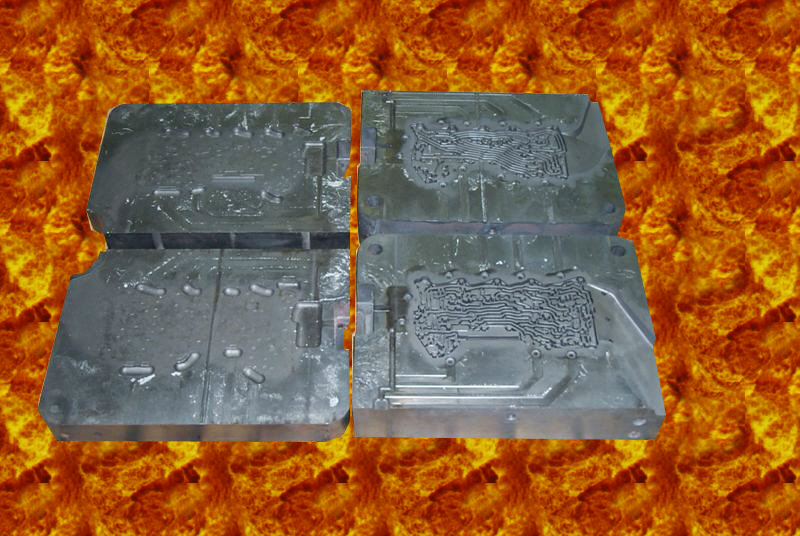
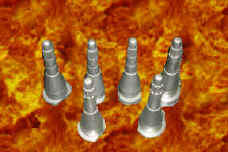
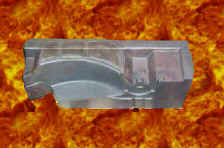
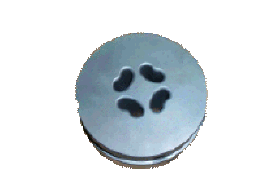 |
|
|