Javascript DHTML Drop Down Menu Powered by dhtml-menu-builder.com
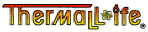
Decreases Die Casting Die Soldering and
Galling
Recent studies, from 2006 and continuing into 2008 by various labs
and organizations, have found that one of the many causes of soldering is due to
the impingement of aluminum to the die steel. Soldering effectively weakens the
steel. Other contributing factors are temperature, wettability, and metal velocity.
To make a bad situation even worse, aluminum
(Al) and iron (Fe) have a natural chemical affinity to one another because of
their makeup and electron imbalance. When contacting each other, they
want to form intermetallic compounds as shown in the photos below and drawings
at the right. When the soldered area is removed, iron from the steel
is also decreased and affected.
ThermaLLife
forms a compound layer barrier that prevents the interaction of the
aluminum (Al) with the iron (Fe) component of the tool steel. Thus the
stages of destructive soldering are stopped before further damage to the
tooling can occur.
Stage |
Description |
Cause |
I |
Erosion of grain boundaries |
Weak regions - cavitation |
II |
Pitting of die surface |
Loose grain - cavitation |
III |
Formation of iron-aluminum compounds |
Chemical - electron imbalance |
IV |
Formation of pyramid shapes |
Rapid diffusion of iron |
V |
Adherence of Aluminum |
Cracks in surface at pyramids |
VI |
Erosion pits |
Cavitation loss of yield strength |
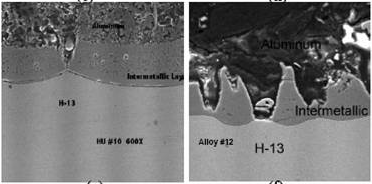
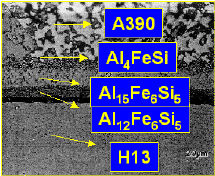
Intermetallic elements of soldering
Loss of the
tool's protective surface or lubrication barrier between the die and cast molten metal
allows the
creation of intermetallic compounds that cause a chemical adhesion or
soldering of the metal to the die's surface.
Related Topics
> - Compression Benefits |