Javascript DHTML Drop Down Menu Powered by dhtml-menu-builder.com
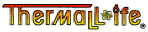
Summary
Our diffusion process is a proprietary
form of ferritic nitrocarburizing performed in a vacuum assist environment.
By a batch process, tool steel is heated to a safe temperature that is well
below the final temper of the tool so final hardness is not affected. Once
heated, uniformly, a mixture of gases are introduced under pressure with the
tooling experiencing the temperature, pressure, and gas environment for a
prescribed time.
Each type of steel receives a different
combination or recipe of these parameters. The gases contain both Nitrogen
and Carbon atoms. A thermo-chemical reaction occurs whereby a sub-zone and
a compound layer are created as nitrogen and carbon atoms are diffused into
the steel’s surface. The diffusion zone is resistance to wear and
corrosion.
The depth of diffusion can be anywhere
from .004”-.006” (102 to 203 microns) depending on the recipe used. The
compound layer is both hard and much thinner .0002” to .0008” (5 to 20
microns) and somewhat ceramic in nature. This compound layer is about 1200
to 1500 vickers in hardness. If you try to abrade the steel with a 65Rc
common file, it will not damage a
ThermaLLife
processed surface. The compound
layer forms a barrier that prevents soldering of aluminum to die cast die
surfaces.
Related Topics
> - Benefits |