Javascript DHTML Drop Down Menu Powered by dhtml-menu-builder.com
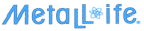
Buffers Cavitation Breakout Effect
Almost all
High Pressure Die Casting dies experience cavitation. This often
occurs in or the near Gate area or other locations of metal flow where the
local pressure suddenly falls below the vapor pressure of the molten metal.
Since we have
processed more than 100,000 die inserts and tooling during our 28 years,
we have also seen more distress failures of this nature than anyone else in
the industry.
A paper on this
phenomena was presented at the 2010 Casting Expo in Florida. The paper
shows why cavitation occurs, and how it can be reduced and buffered.
This destructive force is just
now beginning to be acknowledged and studied by the die casting industry.
The cavitation force
and frequency is what causes these pit marks. Usually these pit marks grow
to become stress concentration points from which cracks can propagate.
Some pit marks, however, stay as pits without crack lines propagating from
them. So heat checking can occur with of without these pits.
From our experience and observation, far too often the two go together.
These pit marks in
the die steel show up as round raised rough areas on castings. People
that have been in die casting for years, mistakenly still attribute
exacerbated heat checking (thermal fatigue) to the creation of these pit
marks.
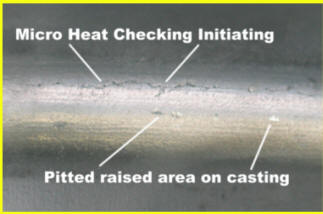
Pitting of the die causes
raised small bumps on casting
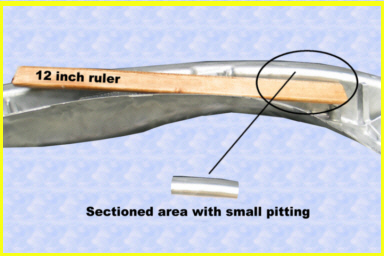
Smaller die pits, if caught early enough, can be corrected
This distress
results in higher die casting costs, either through the need for casting
rework (to remove the risers on the casting) or increased casting scrap
rates. In the worst case, repair or retirement of the die occurs.
Welding of these numerous pitted areas is not effective so many times the
dies need to be re-sunk to get below the breakout.
As
previously stated, the cavitation inception occurs when the local pressure
falls sufficiently far below the saturated vapor pressure of the liquid...a
value given by the tensile strength of the liquid.
Small low pressure vacuum
bubbles collapsing on the surface of the steel with extreme force and
rapidity create high energy "jackhammer" like shockwaves leading to steel
fatigue and breakout. Although it is hard to conceive, the vacuum
vapor in the bubble at collapse has been recorded to be 5,000 kelvin (8,540
F or 4,727 C) which is close to the surface temperature of the sun (5778
kelvin). At the same time pressures of several hundred atmospheres of
pressure (4500 psi) are exerted on the nucleating surface at the same
location with each shot.
MetaLLife
increases the
steel's fatigue strength of die steel by inducing a high value of compression
that can be as much as .018" in subsurface depth. Cracks of pits do
not start in a steel surface that is in a compressive state. Steel has
to go into tensile stress before it yields to fatigue.
This
MetaLLife
surface is textured. This surface
retains lubricant as well as changing the flow characteristics of the molten
metal. Buffering is accomplished when the bubbles collapse, not on the
steel, but on the lubricant or flowing metal that is present on the
textured surface. The buffering surface is replaced with each shot.
This integral renewable shield absorbs the implosion energy from the
collapsing bubbles which is then quickly healed with each shot.
No other die surface engineering
treatment besides
MetaLLife
and
TooLLife
can provide these two benefits.
Unfortunately
cavitation cannot be totally eliminated, however, these high energy
vacuum bubbles can be buffered. By increasing the steel fatigue
strength and causing nucleation (collapse) on another surface other than the
steel surface, the cavitation effect is buffered. Diesel engine coolant cylinder liners use the
buffering method to reduce cavitation effect to cylinder walls.
Whenever the
high velocity molten metal flow path is disrupted to cause the vapor
pressure to drop below local pressure, cavitation results. This
includes a sudden change of flow direction or obstructions to flow.
Examine your dies and see if your breakout and washout are in these areas.
To see papers, videos, and slide presentations of these forces and how they
occur in nature and the industry, visit our section.
Resources.
The
phenomenon of metal breakout is not new and
occurs in other industries besides die casting. Often it is
experienced in pumps, turbines, diesel engine cylinders and other products
such as boat propellers. The boat propeller will literally be eaten
away over time without being subjected to any type of outside abrasive or
destructive environment other than water.
Related Topics
> - Improves Metal Flow
|