|
|
Javascript DHTML Drop Down Menu Powered by dhtml-menu-builder.com
.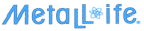
Customer Testimonials
Javascript DHTML Drop Down Menu Powered by dhtml-menu-builder.com
Letters - Over 100,000 dies processed
since 1983.
Our testimonial letters are coded
to protect our clients security)
Specific 20 year endorsement of
MetaLL ife
Dramatic Improvement in Tool Life
(#670 3/07/09)
Less
sticking soldering and drag of die casting
Improved
magnesium flow
Reduced
buffing and polishing time of casting
Reduced
die casting pressure - testimonial letter
Field Result
Comments - Preceding # is internal ref number for
customer.
(Our customer comments are
coded to protect our clients security)
Improved
performance and extended life
Die
casting dies for brass
Die casting Bronwite brass (NEW #670 03/2009)
Crack
closure and prevention
Soldering problems resolved or reduced
Reduction in gate erosion
Better Paint Adhesion
Reduction in porosity problems
Drawing field tests
Blanking and cutting tools
20 year endorsement of
MetaLL ife
#882 - WI - I have been a satisfied customer of Badger Metal Tech
for nearly 20 years.
MetaLL ife
consistently delivers on its promise to substantially improve tool life in
zinc, aluminum and magnesium die cast dies. In brass die cast tooling,
regular use of
MetaLL ife
coupled with proper tool steel selection/application and heat treat process
increased tool life EXPONENTIALLY!
Jerry and his Badger Metal Tech, Inc. staff are extremely helpful and always
available for any type of support needed.
MetaLL ife
works because it's principle is founded on solid physics and metallugical
facts.
Thank you Badger
Metal,
Greg Flint, P.E.
Return to top
Significant improvement in tool life and die performance
#670 -
CA - In the middle 90's we were producing thin wall castings from 380.1 aluminum
alloy for Vendo - a vending machine manufacture - running over 520k parts per
year on two (2) cavity die cast dies. One die produced a gage bar and the
other produced a gate. Before we started a
MetaLL ife
maintenance program with Badger Metal we were averaging 180k shots. After these
the dies were replace due to heat checking. The replacement costs for each
die was $30,000.
After approval by the customer, new dies were built and then immediately after
sampling received
MetaLL ife.
This was done, as recommended by Badger Metal again at 75k and every 100k shots
thereafter for the life of the tool. We then cast 420k shots on each die
before replacing the cavities. Casting quality was improved with far
less scrap/re-melt required.
#670 - CA - The success
encouraged us to try on an eight cavity die for a brass (Bronwite C99750 alloy)
to cast Weather-Tec impact sprinklers for the irrigation industry. This is a
brass alloy that has 60% copper and 18% manganese with a melting point at 1550
degrees. Each part
weighs about .20 lbs. Prior, we could expect 100,000 shots
before die replaced. We have been using the
MetaLL ife
process on these dies now for over 15 years and average 200k shots on the
tooling before replacing the cavities. Lamar tool and die casting has
other customers that request that we apply MetaLL ife
to there tooling with great improvements in die life.
Badger's service is
outstanding. They are well aware of the small window regarding turn around
that is needed to meet production schedules. We continue in 2010 to use
their services with a high degree of confidence.
Larry Snoreen - Owner and
General Manager
Return to top
Less sticking, soldering, and drag
#481 - AR - Very pleased with performance of tooling for parking meters that
we did for him. Dies no longer stick, solder, or drag. Also noticed that the
heat checking on the older tools is considerably reduced with much better
casting appearance. Flow is also improved. Plans on continuing to send us
tooling as soon as production schedules free up. So impressed were they that he
sent us a LETTER praising our process and service received. Quoted as follows:
"We have recently procured the services of Badger Metal to do
maintenance work on three (3) of our dies. Most specifically, the cleaning of
these dies and the
MetaLL ife
process provided by Badger. I would like to take this opportunity to express the
highest of praise to Badger Metal for the excellent services and outstanding
quality of workmanship they provided to #481 Incorporated. Turn around time
between shipment for maintenance on the dies until the time they were resumed to
us, finished; was swift and very much appreciated by all concerned (our need to
have these dies in-house is always a concern).
I was very impressed as well as 100% satisfied with every aspect of the services
that we received from Badger. I look forward to our future business dealings
with Jerry and would highly recommend Badgers' services to any potentially
interested customer."
Charlie #481
Manufacturing Plant Manager
Return to top
Reduced Casting Pressure
#299 - MN - The customer told us that after using our process for some time
he decided to try using it on a die that was giving him fits with filling.
Besides the filling problem disappearing, there was no soldering, no cracks in
the casting, and no flashing as before. He was also able to reduce his casting
pressure by 30%. The casting also looked much better with a reduction in flow
marks. Here is the customer's follow-up letter that we received:
Dear Badger Metal:
This letter is being sent to you in regards to the results of your
MetaLL ife
treatment you applied to our mold that produces bracket , part #505-297.
Enclosed:
1. One part as cast with runner and spills attached
2. One part marked B (For before
MetaLL ife)
machine pressure to fill 1500 PSI.
3. One part marked A-(After
MetaLL ife)
machine pressure to fill 1050 PSI.
The
MetaLL ife
process has allowed us to use a much lower pressure to fill the bracket.
The mold is parted with 3 cam pulls. Lower pressure has allowed us to run this
mold 2000 shots before pulling the tool and cleaning cam slides. With the higher
pressure we could run the mold only 200 shots before pulling the tool and
cleaning flash from cam slides.
Once again,
MetaLL ife
Process has enabled us to increase production on this mold and many others you
have done for us in the past. Thank you once again Badger Metal Tech, and thank
you
MetaLL ife.
Sincerely,
Tom Dousette - Vice President #299
Tom went on to tell us that
the World Cup Sailing Teams now use a Shark Skin finish on the hulls of all of
their boats to increase their speed. He feels that this same type of
finish obtained from
MetaLL ife
allows him to improve his casting process capabilities. We know that a
MetaLL ife
surface improves the flow and reduces porosity concentration. We have not,
however, investigated how reduced die pressures would assist in even further
increases in tool life. Not as yet we haven't.....
Return to top
#25 - KY - After seeing immediate improvement in the performance of a large
magnesium die casting die and its flow characteristics, this firm sent by fax
the following comments thanking us for a job well done:
Dear Mr. Skoff,
"I would like to congratulate you and your entire staff for a job well done. The
dedication to completing the work on the instrument panel cavities on such short
notice have proven Badger to be a "World Class Supplier". Thank you for your
efforts."
Sincerely,
Dave #25
Tool Engineer
Return
to top
Less sticking, soldering, and drag
#481 - AR - Very pleased with performance of tooling for parking meters that
we did for him. Dies no longer stick, solder, or drag. Also noticed that the
heat checking on the older tools is considerably reduced with much better
casting appearance. Flow is also improved. Plans on continuing to send us
tooling as soon as production schedules free up. So impressed were they that he
sent us a LETTER praising our process and service received. Quoted as follows:
"We have recently procured the services of Badger Metal to do
maintenance work on three (3) of our dies. Most specifically, the cleaning of
these dies and the
MetaLL ife
process provided by Badger. I would like to take this opportunity to express the
highest of praise to Badger Metal for the excellent services and outstanding
quality of workmanship they provided to #481 Incorporated. Turn around time
between shipment for maintenance on the dies until the time they were resumed to
us, finished; was swift and very much appreciated by all concerned (our need to
have these dies in-house is always a concern).
I was very impressed as well as 100% satisfied with every aspect of the services
that we received from Badger. I look forward to our future business dealings
with Jerry and would highly recommend Badgers' services to any potentially
interested customer."
Charlie #481
Manufacturing Plant Manager
Return to top
#25 - KY - After seeing immediate improvement in the performance of a large
magnesium die casting die and its flow characteristics, this firm sent by fax
the following comments thanking us for a job well done:
Dear Mr. Skoff,
"I would like to congratulate you and your entire staff for a job well done. The
dedication to completing the work on the instrument panel cavities on such short
notice have proven Badger to be a "World Class Supplier". Thank you for your
efforts."
Sincerely,
Dave #25
Tool Engineer
Return
to top
Improved magnesium and aluminum
metal flow
#31 - IL - A
problem of flow due to the configuration of the casting and tool was preventing
good fill. The problem was eliminated after topography modification with a
special
MetaLL ife
process.
Return to top
Reduced time of buffing operations
#0857 - IA -
Received via email
Paul,
MetaLL ife
has been an excellent answer for us. It has eliminated many buffing
operations, and increased my die life. Thanks for all your help. Early
this summer you will see more new cavities.
Erik Hansen #0857
V.P. Manufacturing
#274 - WI - After
applying
MetaLL ife
to a small barber utility tool, we were notified by our polisher that the
casting was taking less time to buff due to a reduction in hidden porosity
and better casting fill and surface characteristics. The cosmetic
requirement of this tool was such that the slightest imperfection in the
surface would show after painting which was unacceptable.
MetaLL ife
got rid of this concern.
Return to top
Die Casting Dies for Brass
-
#870 - CA - We use
MetaLL ife
on small brass dies sprinkler head die casting dies. Successfully have
repeated the process on both NEW and USED versions of these multiple cavity
tools to stop/close existing heat checking. Continued life extension
improvement by adding this process to tooling. We and our end user sees
improved parts with less heat checking.
-
#670 - CA - Use on brass dies and see major
improvements in life and performance on these tools. Now starting to use on
Aluminum dies for same reasons.
-
#626 - FL - Dies we processed for were previously
running brass parts and had extreme amounts of heat checking. After processing,
the dies looked so good we used these same tools to run zinc parts. Appearance
of the zinc casting is quite acceptable for our product. #626 is a captive
house.
Return to top
Improved Performance & Extended Life
-
#792 - IN - At 70,000 shots after
a
MetaLL ife
treatment on ejector side, and
MetaLL ife
+
ThermaLLife
on the cover side, the die continues to perform and has already out lasted
the normal life cycle where they would begin to have down time for repairs and
polishing to remove solder buildup.
-
#872 - IL - This customer has
been able to increase their tool life for a sensitive automotive part ten (10x)
fold by applying followed by
ThermaLLife
after final sampling on NEW tooling.
-
#150 - MN - Dies are running extremely well,
however, before
MetaLL ife
their production manager said the dies could not be used anymore and would have
to be retooled due to excessive casting leakage problems, and sticking with
soldering. Casting appearance has tremendously improved.
-
#576 - PA - We definitely helped extend the life
on the OLD bowl die. Customer and end user are pleased. Will continue to do more
tooling.
-
#569 - KY- Very pleased with the transmission die
we did (2 cavity). Said die is running and has not stuck or broke a pin.
Customer now wants to do Cav #3,4.
-
#415 - IL - Have seen significant improvement in
die performance since starting to use
MetaLL ife.
We plan to use
MetaLL ife
on all of his tooling in the future.
-
#691- CANADA - The die ran great. Before we did
MetaLL ife,
the die was totally unusable. Afterwards, we were able to run the die
19-20hrs/day 7 days a week with no problems. The die ran so well that we got 3
weeks ahead on production requirements. Now he will look at other tooling to do.
-
#039 - AR - We have set up a schedule to do
MetaLL ife
on all of their BIG runner dies every 30,000 shots. Seeing considerable benefit
to casting appearance by incorporating
MetaLL ife
as a schedule maintenance procedure.
-
#590 - FL - The first scale housing (#1786) ran
much better. Castings required much less rework. Also appeared to be some
improvement in the flow characteristics.
-
#150 - MN - Customer continues to be pleased with
results of doing the cattle tagger dies. Prior to our processing these dies he
and his customer thought that new tooling might be necessary. This is no longer
the case since the dies are holding up extremely well.
-
#659 - AR- Did a zinc die that had been welded
and was not buffing out well. We did T-21 which gave them a 60Rms finish before
buffing. The parts buffed out much better than before. Customer is very
satisfied.
-
#150 - MN - said the cattle tagger die we did in
May is doing exceptionally well after 3 runs. Their customer is pleased that he
did not have to buy a new tool which was the altemative that was being
considered if he had not found
MetaLL ife.
-
#704 - CA - Vendo die is running better than ever
after
MetaLL ife.
Shot rate has increased from 125/hr to 130/hr. Castings look great with a low
reject rate of .05%. Considering for other high run tooling.
-
#609 - TX - The last DET 38 endbell (new die) we
did in Nov 95 has been running since Dec 95 at a rate of 1K/day and now has
about 40 weeks of run time = 200K shots on it with still no heat checking. Have
noticed vast improvement in casting appearance and flow characteristics.
Return to top
Crack Closure and Prevention
-
#032 - Toby Parks TX - New
tooling for air conditioner component casting would heat check after only 5,000
to 10,000 shots. After
MetaLL ife
no heat checking in this time frame.
-
#753 - CA - The PR3 handle that he wanted to
improve appearance if possible 50%, looked so good (at least 90% improvement)
that he is going to send us an after casting that we can use in our advertising
if desired. We have made believers out of the other owners of the company. For
the future will consider
MetaLL ife
instead of building new tooling.
-
#039 - AR - Primary reason for doing
MetaLL ife
is to benefit from longer runs with less downtime and tool repair from heat
checking. Cost of
MetaLL ife
pays for itself by this factor alone. They schedule redoing
MetaLL ife
at every 30,000 shots, scheduling permitting.
-
#321 - CA - The recent chair die mold that we did
(both cover and ejector) is running much better parts with no signs of heat
checking mirrored on the part. The die shows that the cracks are closed. Very
satisfied. Sending more castings to quote.
-
#674 OH - Ran the first set of covers we did for
one week with no problems and cracks stayed closed. Also the die seemed to hold
lubricant much better. Pleased and now wants to do the ejector sides.
-
#542 - IN - says that the previous spider die
would only get about 10,000 shots before it starting to heat check all over.
Since doing
MetaLL ife
to a new set of cavities, now has 30,000 with no heat checking. We processed
this too when the die was new after about 3500 shots.
-
#705 - MEXICO - The first iron sole plate dies we
did now have about 20,000 shots on them with no new heat checking. Patrick is
pleased with the performance of the tool and plans to do it again once he
reaches 50,000 shots.
-
#760 - CA - Cosmetic appearance is one of the key
selling features of their vacuum cleaners. Heat checking on the die requires
costly secondary operations.
MetaLL ife
closed up the heat checks and allowed the tool to produce the necessary quality
castings which reduced the customer's secondary costs.
Return to top
Soldering using
MetaLL ife
or (MetaLL ife
+
ThermaLLife
-
#704 - CA - The combination of
MetaLL ife
(T-41) +
ThermaLLife
reduces or eliminates soldering problems.
Cores tested had an established history of soldering immediately after only a
few shots or while the die was being sampled. Now they are able to run over 1000
shots without any soldering or indication of breakdown of the coating. Have
processed both small (1/2" to 5/8" dia) and large (3" dia) cores with equal
success.
-
#042 - MO - The customer eliminated solder
problems on Allied Signal cores that normally would experience build-up after
only approximately 900 shots. Two sets of cores were
MetaLL ife
+
CrN coated
(processed T-21 & T-41). Cores now have 15,000 shots with still no solder or
build-up. It is interesting to note that during one of the production runs that
the water was accidently shut off to the cores, however, the resulting build-up
was minor and cleaned itself when the water was turned back on and lubricant
reapplied to the die.
-
#054 - IL - Two cores were processed with
T-41
MetaLL ife.
These cores would historically solder between 12,000 to 13,000 shots. These same
cores are now at 55,000 shots without any soldering. The two cores (2.75" dia x
6.2") were processed in May 1996.
-
#032 - Toby Parks TX -New tool sticking was
always a problem on CFN cores because they have a zero to 1/2 degree draft.
Would need to polish in draft to try and prevent this from occurring. After
MetaLL ife
with our T-21 process, their initiation stick problems dropped from 100% to 0%.
Have since expanded use to inserts as well as more CFN cores.
-
#670 - CA - The 3500 Pelco dies are now running
after
MetaLL ife
without any soldering problems. This die because of the protruding ear always
soldered. Die cast machine operators are extremely pleased with this problem
being eliminated. Same results on the Vendo Uni-Gage dies we recently did...No
more solder problems.
-
#406- Ray Meyers OH - Still using the cores we
did. Before he was having to change the cores twice per week. Now he runs about
8 weeks without touching them. He prefers the
MetaLL ife
and will be sending us more heat treated ones as soon as he has some.
-
#719- CA - (ZINC) impressed with the performance
of the core pins we did. Not only did they not solder, but they also has a
condition in the die which stressed the pins but only damaged the untreated
pins. The
MetaLL ife
ones did not show as much damage. Also the first 2 weeks after our pins were
installed, the die ran phenomenally well with no soldering.
-
#032 - Toby Parks TX - His customer is "tickled
pink" with our T-41 process that we did on their ejector cores. Much less
expensive than going with an acid etch according to Toby. Also running with much
less problems. Has more to send to us.
-
#710 - OH - First parts are looking good on the
small zinc "Z" fitting. Parts are not sticking as before.
-
#664- CA- The heatsink die we did for him earlier
this month is turning our much better parts. No more sticking in the fin areas.
Also pleased with the way the heat checks are closed. Casting has a much better
appearance. Appreciated our quick turn around service (Accelerated Delivery) he
requested.
-
#671 - CO - Have been using the process since
August 1990 and would not think of running any of my tooling, whether NEW or
USED, without first putting
MetaLL ife
on the dies before I do any coating. Currently we use the Futura coating
(Titanium Aluminum Nitride - TiAlN).
Return to top
Reduction in Gate Erosion
-
#001- Wl - Kevin said that the
blower housing after
MetaLL ife
eliminated a second operation for cleaning up the gate area which prior to
MetaLL ife
posed a handling problem. Very pleased with both physical appearance of casting
and how long the improved condition has lasted. Also said that boat motor dies
are working so well that this is the first time they have not had to weld them.
Usually every 5K shots they are welding the fin area. They have done 3-4 sets of
these tools with
MetaLL ife
and all are performing equally well. Try to do every 20K shots. Die performance,
life, and casting appearance has improved considerably.
-
#001 - Wl - The boat motor die that we have
repeatedly processed with
MetaLL ife
has made it through a complete production run without any welding required on
the die. According to this customer, this is the first time that they have ever
been able to run this tool for a full production run without having to weld the
tool
Return to top
Reduction in Porosity Problems
-
#693- OR - Is an end user of die castings. Since
we did our gearbox lid and housing, we have noticed a tremendous improvement in
the casting appearance with less porosity and pitting problems.
-
#30 - OH - The used transmission slides we did
worked out well that they got the additional life they needed from this die
before replacing with a new tool. Now considering doing on their new tool.
Return to top
Better Paint Adhesion
Return to top
Draw Forming Field Tests
-
#91 - IL - Applied to CPM10V draw
cap. At most would get about 60K before tool would gall and have to be
polished or replaced. Applied first the
MetaLL ife
process and followed this with
Balzers TiCN coating.
Micro pockets were questioned upon return to the customer with concern about
these causing more py blems than they already had experienced. Customer
was assured and tool was installed and ran 4,000,000+ parts. Engineer has
since left the company and is using
MetaLL ife
at his new employment facility.
-
#498 - WI - has been enjoying the
MetaLL ife benefits
since the late 80’s when their toolroom manager came across an ad in a leading
trade journal. They performed a trial in 1987, on a high volume draw and pinch
trimmed part and witnessed their "parts till polish" increase from 10,000 to
80,000 pieces. John Matteson now regularly use the process on all draw
rings. When necessary, they can polish three to four times without having
to retreat their tooling using a 600 abrasive paper and light oil. For severe
applications, such as brushed #304 stainless, he uses it as a substrate
preparation for an additional TiCN coating since they know
MetaLL ife
will not peel or chip.
-
#528 - Wl - Customer called back
to say that the
MetaLL ife
solved his galling problems when forming 1/8" stainless. Extremely pleased with
results.
#935 - IL - Uses on D2 and CPM tooling to reduce scoring of the produced parts.
MetaLL ife allows
them to run over 6000 pieces as opposed to only a few before galling and scoring
of both the die and part would occur.
-
#680 - OH - Ran complete job of
38,000 parts with no galling or build-up on die. Now in the process of redoing
all their tooling with
MetaLL ife
v/s chrome plating.
-
#680 - OH - So far has run 18,000
draw parts on a die that prior to
MetaLL ife
was impossible to run as little as 200-300 parts without galling up. Parts are
better than he has ever seen off this tool. Had been using chrome plating with
no success. 'Very, very, pleased." Saved him from losing us customer.
-
#669 - NJ - The set of rectangular draw dies that
will did now have run 60,000 pcs with no pick up problems of any kind. Prior to
our process, they were having problems with galling and pickup on the comers.
-
#788 - IL- Our customer is getting their best
runs ever they have ever had with the draw ring we processed for their
application.
-
#213 - OH - The lower form die we did went from
30K to 200K parts before any redress. Overall this resulted in over a 200% life
improvement.
Return to top
Blanking, Punching and Perishable Cutting Tools
-
#46 - WI - A large stamping ring
was picking up and galling after only a few strokes. After processing this
problem has disappeared except for one small area where they had inadvertently
polished the die.
MetaLL ife
was reapplied to the area and the die runs without problems.
-
#099 - WI - Was having their hobs
coated. Started to have a problem with chipping of the edge when
resharpening and during use. Now enjoy all of the
MetaLL ife
life extending and fatigue resistance benefits of coatings plus the added cost
saving extra of not having to recoat when the hobs need to be resharpened.
-
#922 - WI - Uses
MetaLL ife on
dies for blanking automotive and water heater parts in both compound and
progressive configurations. Customer says the treated punches run about
30% longer with much less downtime. They also like how re-sharpenings can
be done without removing the improved fatigue resistant benefits.
-
#661 - NY - The worm roll dies we
did got 4600 parts before they chipped. Normally they expect around 1700-2000
pcs before chipping occurs. He also said that even the astounding 4600 piece
figure was not a fair test because the machine these were used on had bearing
problems. Had it not been for this problem the
MetaLL ife
worm roll dies would have gotten even more than 4600 pcs.
-
#680 - OH - Customer has
been using the
MetaLL ife process
for over 10 year on their progressive blanking and piercing tooling.
The problems they had with chipping on their punches and dies when used on
martin site material just disappeared once
MetaLL ife was
tried.
-
#063 - MN -The CPM M4 and D2 punches that we have
been doing for him since 1989 are resisting fatigue edge cracking and chipping
allowing longer runs. They are using these to stamp out 303 stainless steel
parts for the medical industry. Nothing else he has tried works like the Metlife
T-10 process.
Return to top

Related Topics
> - Field testing
ThermaLLife |
|
|
|
Photos are
DIE SURFACE ENGINEERING
PREVENT AND FIX DIE FAILURES IN DIE CASTING DIES, DRAWING FORMING STAMPING, AND PLASTIC MOLDS.
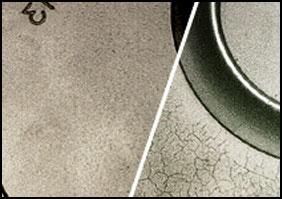
After and Before
MetaLL ife
treatment
Send us castings to receive
Free Quotes & Consulting
within 24 hrs
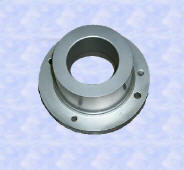
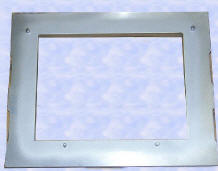
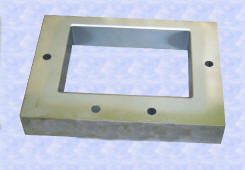
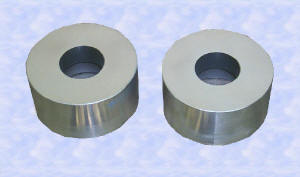
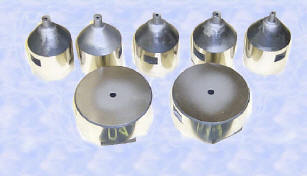
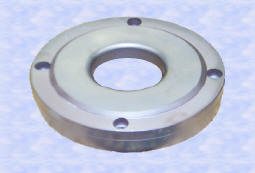
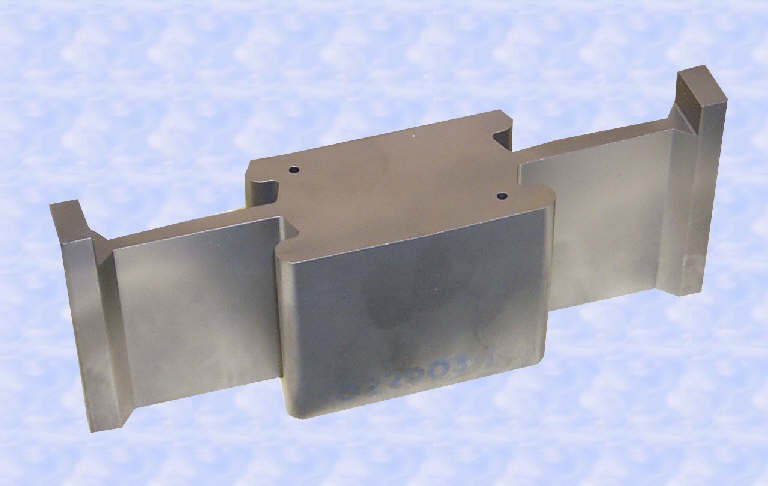
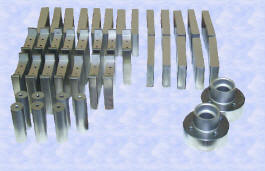
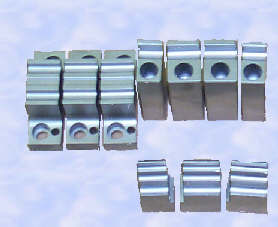 |
|
|