Javascript DHTML Drop Down Menu Powered by dhtml-menu-builder.com
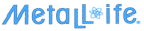
Reduce Casting Porosity
Trapped gases
in castings are one cause for porosity to develop. This is more prevalent
in high pressure die cast castings. Some porosity is inherent in the
casting process. Porosity can also be caused by internal shrinkage,
oxide films, inclusions, etc. The presence of casting porosity does not
always render the casting defective.
Texturing the surface, as is often
done to magnesium dies, improves flow, prevents cold shot or flow marks and
reduces the concentrated areas where porosity can occur. Magnesium die
castings are more prone to this phenomena because of the thinness of the
walls. Aluminum die castings sometimes will experience porosity due to
how the metal is introduced into the die and the final configuration of the
tool.
MetaLLife
improves flow so that the "porosity causing" trapped gas
bubbles are more homogeneously distributed in the
casting as opposed to being concentrated in one area.
MetaLLife,
by it textured surface, has a buffering
effect on cavitation.
This unique attribute increases tool life by reducing breakout and
erosion of the die steel.
Castings that are
produced by permanent mold or squeeze or semi-solid processes, have less
tendency to have porosity problems producing more dense, thicker wall
components for pressure applications or those requiring extra strength.
Related
Topics >
Better Casting Appearance |