Javascript DHTML Drop Down Menu Powered by dhtml-menu-builder.com
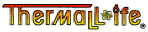
Increases Wear Resistance
ThermaLLife
is a chemical diffusion process whereby the tool steel is heated to a
subcritical temperature and gases are introduced into the environment.
The gases have both a carbon and nitrogen element.
With added atmospheric pressure, the Nitrogen and Carbon gas atoms are
diffused into the surface of the tooling. With this a small sustained
value of beneficial compressive stress is added along with a compound and
diffused zone.
The diffusion layer for die casting dies is about .004”-.006” in depth with
a compound layer of .0003” to .0005”. The compound layer is the function
aspect of the process that prevents soldering in most die casting
applications. This layer forms a barrier between the aluminum and iron that
prevents the covalent electron bonding of the two elements, leading to a
soldered condition. The increased fatigue strength comes from the created
compression curve. The nitrogen and carbon atoms, that are diffused into the steel,
stretch the surface and create the opposing layer of compression.
The hardness is
measured in Vickers (1200-1500) since normal Rockwell readings penetrate
through the thin diffusion zone. This Vickers reading, if approximated to
HRc would be about 65-75. The compound layer hardness is usually in the
range of 1000 Knoop (10g). The photo at the right shows diamond marks.
These are micro hardness readings of the diffusion zone. The smaller
the diamonds, the harder the material.
This combined hardness
makes the FNC material more resistant to wear, erosion, and scuffing. Both
the diffusion and compound layer are effective combinations to ward off
corrosion, oxidation, and soldering.
Related Topics
> - Reduces
Soldering |