Javascript DHTML Drop Down Menu Powered by dhtml-menu-builder.com
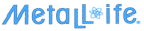
Cosmetic Appearance
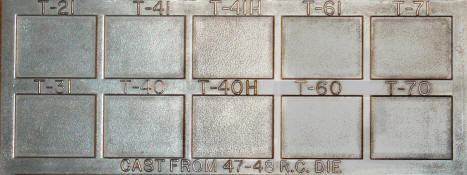
This side of the tooling for making this casting was
manufactured from H-13 material and then processed with each of the noted
MetaLLife
processes.
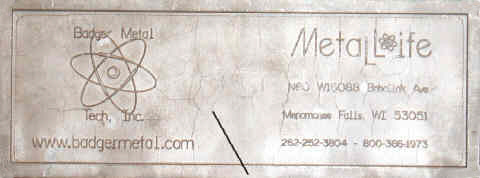
This side of the tooling for making this casting was
purposely manufactured from a P-20 material so that typical heat
checking would show after only 1200 shots. This die surface received
no
MetaLLife treatment.
In 2006, Case
Western University studied the effect of retaining lubricant on the surface
of a die. Their finding showed that residual die lubricant film
insulates the surface of the die from direct contact with the molten metal
thus lowering the maximum surface temperature. Experienced temperature
drop due to die lube residue on a flat surface reached 400 degrees F after
15,000 cycles. This reduces thermal stresses at the surface of the die
which promotes longer die life.
The thickness of the residual die lube layer on a flat
surface is not uniform and dependent on orientation and spraying variables.
Compressive topography assures better uniform lubricant
retention and better fatigue strength.
These
findings were confirmed by Case Western's standardized dip tank test.
The complete report is available in our password protected Die Materials
Committee Resource section.
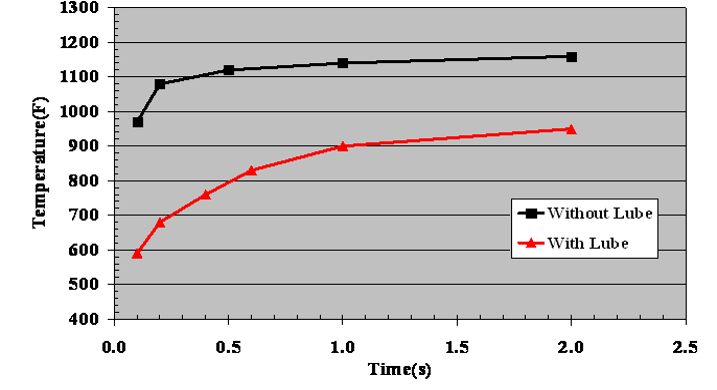
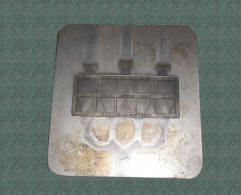
Cover - H-13 |
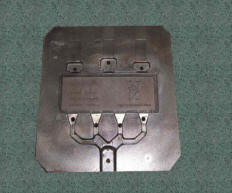
Ejector - P-20 |
Above photos show
the inserts that were treated
with the various
MetaLLife
processes |
|
Click for larger view
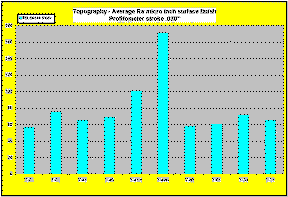
Average Ra Micro Inch Finish .030" travel
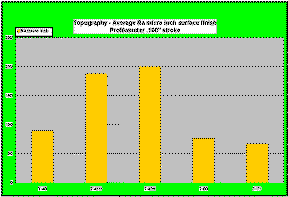
Average Ra Micro Inch Finish .100" travel
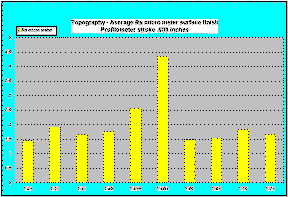
Average Ra Micro mm Finish .030" travel

Average Ra Micro mm Finish .100" travel
See
Specs Compression Curves
|